Revolutionizing SCADA Systems with IoT Technology: Unlocking New Business Opportunities
What is a SCADA?
SCADA is a centrally connected system that monitors the plant processes at every point. It allows the managers to track information coming in from equipment and customize, operate, and perform other functions within an industry. It is software that gets installed on a computer, and one of its essential roles is to act as a communicable interface among industrial machines.
SCADA systems generally use when combined with PLCs and other devices, and PLCs may become a part of the SCADA system for effective operations. If SCADA and PLCs perform together, they form an automatic system to allot maintenance tasks that form the core of a predictive maintenance program. Here’s how it works:
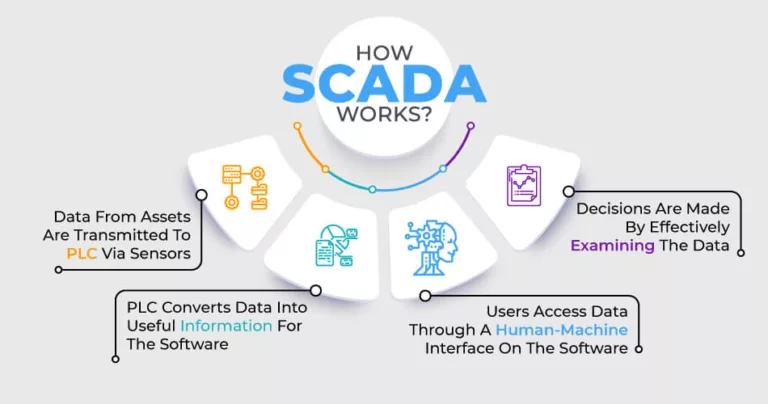
• Data from assets are transmitted to PLC via sensors
• PLC converts data into useful information for the software
• Users access data through a human-machine interface on the software
• Decisions are made by effectively examining the data
IoT
The Internet of Things has become a sensation for businesses to progress in multiple areas. It adds to the value and image of the brands with its automated functionality and advanced functioning. Using sensor devices to turn assets into automated machines/equipment is bringing a new transformation in the industries regarding profit and quality production.
The existing systems had many challenges, like inaccurate reports, mismanaged data, and more employee involvement. To meet these challenges, almost all the use cases need to be digitally enabled to see the differences that IoT technology can make for businesses. Hence, sensor-based technology is bringing a rapid transformation to clear out the unwantedness in industries and lay an organized system for quality services.
why IoT Technology ?
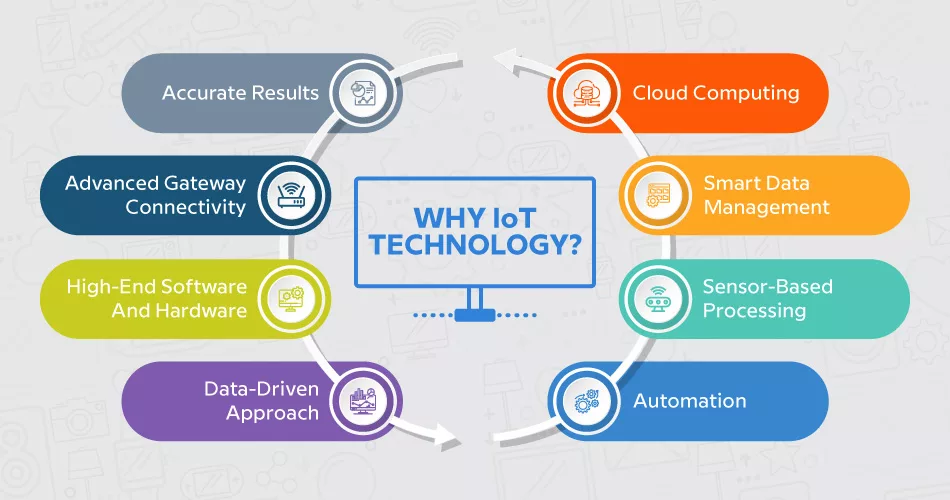
The main challenge for businesses now is to deal with the old and outdated versions of SCADA systems that operate manually. They consist of substantial labor costs and are incapable of providing illustrative reports where precise details mention. This is halting industrial productivity and hindering their growth in all aspects.
The Internet of Things is an advanced concept that provides businesses with the needed options, especially automation & gained productivity. Conventional SCADA systems have played an essential role in improving industrial efficiency, but IoT technology is emerging with more advanced concepts that are useful for businesses in myriad ways.
The use of IoT in different sectors is gaining force every day, and several new organizations are implementing IoT solutions to improve operability. It eliminates the day-to-day challenges in the industries with great asset cumulations and data production. Since IoT is a data-driven technology, it is very effective from the business point of view. It provides:
- Accurate results
- Data-driven approach
- Advanced gateway connectivity
- High-end software and hardware
- Cloud computing
- Automation
- Sensor-based processing
The Internet of Things is transforming businesses by benefiting them with technical solutions. It is thus becoming a sensation for industrialists as it utilizes the resources well and provides accurate insights, assisting in better decision-making.
How Can IoT Take SCADA Systems to the Next Level?
The growth and acceptance of IoT technology in businesses would redefine a smart and intelligent system that does its job automatically. The presence of IoT would complement SCADA by widening the opportunities and allowing better functioning. With the help of predictable analysis, a data-driven approach, preventative maintenance of the equipment, detailed and organized report generation, and a customizable and personalized user dashboard, IoT-enabled SCADA would reach the new heights businesses have longed for.
With the increasing number of interconnected devices and steadfast growth in connectivity, the data has also potentially increased. To handle such massive data and keep it organized in numerous ways, IoT has to come into action sooner or later. With the inclusion of the Internet of Things as a brand-new concept in industries, performing analytical tasks and automated processing would come into play to render better services. This also provides benefits to managers in simplified information sharing and improved transparency.
It has been almost 40 years since SCADA systems have helped various industries to monitor and manage processes and applications. It has further boosted operational efficiencies and reduced overall costs. But with the advancement in technologies like the advent of IoT, it can be made better along with the needed improvements in equipment efficiency. With SCADA being an end-to-end supervisory system, acquiring data through remote terminal units (RTUs) connected to sensors, IoT is also an end-to-end system that uses advanced sensors to gather data from the assets for smooth functioning. However, with the installation of IoT-powered solutions and transformational attributes of sensor devices, gateways, and user-oriented dashboards, it is high time for industrialists to switch to IoT solutions. The answer can be installed in the existing SCADA system and offers quality services to the owners.
How does a SCADA system benefit from the integration of IoT technology?
The Internet of Things (IoT) is a disruptive technology that utilizes sensors, gateways, and interactive dashboards to improve business productivity across all areas. Unlike the current industrial SCADA system, which is limited to the factory floor and only displays data from within the plant, IoT can significantly enhance data accessibility and operability for various operations in different industries. Integrating IoT technology with existing SCADA systems can equip businesses with remarkable features like scalability, interoperability, and enhanced security for overall industrial processing. Furthermore, IoT can work alongside the SCADA system, transforming the entire SCADA landscape. To get started, it’s essential to identify the right IoT platform that offers a variety of adapters and connectors to integrate with the SCADA system. Here are eight significant benefits of implementing the Internet of Things into a SCADA system.
Overall Equipment Effectiveness (OEE)
The measurement of Overall Equipment Effectiveness (OEE) is a crucial metric for evaluating equipment availability, quality, and performance, whether a single machine or an entire business process. For the past 40 years, SCADA has been widely used in industries to monitor utility networks and industrial operations, providing detailed information on asset performance that enables managers to make informed decisions. However, the integration of IoT in SCADA significantly improves equipment effectiveness by applying real-time monitoring controls and advanced methods for maintenance controls like automatic data extraction, secured data transfer, and idle time collection. This utilization of IoT technology for OEE benefits production in industries and improves how managers retrieve and respond to equipment information.
Machine-to-machine Communication
The Internet of Things (IoT) focuses on machine-to-machine communication, allowing industrial equipment to interconnect via sensors, gateways, and other advanced technologies. By integrating IoT with SCADA systems, machine-to-machine communication can significantly improve, revolutionizing how industries operate. Incorporating IoT into existing SCADA systems enables managers to maintain real-time records of industrial processes more efficiently. Additionally, IoT technology offers quick accessibility through smart gadget connectivity, displaying the relevant details of the preferred device for the specific user. This facilitates efficient plant management and enables on-the-spot decision-making.
Data Acquisition
Integrating an IoT solution with a SCADA system can significantly enhance the data collection process in industries that rely on SCADA. While a SCADA system enables remote human interaction with industrial processes, IoT technology focuses on machine-to-machine communication. As SCADA systems continue to evolve, they will likely transition into IoT systems, providing a more intelligent and well-integrated platform. Therefore, one of the significant benefits of integrating IoT with SCADA is improved data acquisition, which allows for a better understanding and extraction of data. By utilizing the Internet of Things capabilities, data acquired can generate production and utility reports within an industry.
Security
In data-driven production, security is a critical aspect that requires a well-informed infrastructure to manage effectively. Traditional SCADA systems lack systematic security measures, which can be significantly improved by integrating IoT-based solutions such as remote monitoring, anomaly detection, and secured data transfer. This enables server and application protection for the entire process across the data center, reducing the risk of data breaches. Additionally, managers can keep a live track of plant functioning and relevant details through an IoT SCADA system. By utilizing an IoT SCADA system, businesses can add value by ensuring well-monitored assets, secured networks, and assessed risks for better decision-making.
Remote Management and Monitoring
Open SCADA platforms are typically compatible with most OEMs and communicate well with PLCs from any OEM, reducing the likelihood of integration issues. This allows consumers or industrialists to easily customize the entire system, making an IoT SCADA a completely custom-built SCADA system. However, due to increased data capturing, asset owners now demand the integration of predictive algorithms, optimized asset health conditions, and cost savings. Therefore, utilizing IoT solutions for industrial SCADA systems proves efficient regarding plant management and keen monitoring.
Scalability
Enterprises are always searching for ways to reduce excess operational costs. Manufacturing and other essential industries can utilize the scalability and flexibility features to manage their operations effectively. To implement such a system, they require technology-based solutions like IoT technology that provide a scalable platform where necessary. This technology enables the setup of a robust system for industrialists, allowing them to perform better and achieve increased revenue.
Cloud-Assistance
The cloud is a revolutionary concept that involves utilizing remote internet servers to handle large amounts of information. Previously, SCADA systems were managed on local computers, which made it challenging for managers to keep track of various processes. However, with the integration of IoT technology, it is now possible to shift the entire industrial system to the cloud and securely store all information. This enables more accessible access to critical information and simplifies significant tasks for the product handling team by displaying and storing data in real time.
Predictive Analytics
SCADA systems have served their purpose well in the past. Still, with the growing demand for data from consumers, industrialists need to integrate IoT technology to ensure both quality and quantity in their production. Quality is a crucial aspect of business operations as it satisfies consumer demands. Therefore, IoT technology provides an ideal solution for predicting production needs and revolutionizing industries with its machine-handling capabilities and data-driven approach. It helps improve decision-making by providing detailed reports and analyses to assist managers in strategic planning. Overall, integrating IoT-based solutions into SCADA systems enables better production control and enhances the quality of products and services.
Conclusion:SCADA has been the best in their work areas as they brought industry improvements. Still, with the advent of IoT technology, improving the same through automation, predictive analysis, and getting a sustainable solution within the industries has become crucial.
Revolutionizing SCADA Systems with IoT Technology: Unlocking New Business Opportunities Read More »